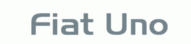
Fiat Uno Manual
Examination and renovation (903 cc engine)Engine / Examination and renovation (903 cc engine)
1 With the engine stripped down and all parts thoroughly clean, it is now time to examine everything for wear. The following items should be checked and where necessary renewed or renovated as described in the following Sections.
Cylinder block and crankcase 2 Examine the casting carefully for cracks especially around the bolt holes and between cylinders.
3 The cylinder bores must be checked for taper, ovality, scoring and scratching. Start by examining the top of the cylinder bores. If they are at all worn, a ridge will be felt on the thrust side. This ridge marks the limit of piston ring travel. The owner will have a good indication of bore wear prior to dismantling by the quantity of oil consumed and the emission of blue smoke from the exhaust especially when the engine is cold.
4 An internal micrometer or dial gauge can be used to check bore wear and taper against the Specifications, but this is a pointless operation if the engine is obviously in need of reboring due to excessive oil consumption.
5 Your engine reconditioner will be able to re-bore the block for you and supply the correct oversize pistons to give the correct running clearance.
6 If the engine has reached the limit for reboring then cylinder liners can be fitted, but here again this is a job for your engine reconditioner.
7 To rectify minor bore wear it is possible to fit proprietary oil control rings. A good way to test the condition of the engine is to have it at normal operating temperature with the spark plugs removed. Screw a compression gauge (available from most motor accessory stores) into the first plug hole. Hold the accelerator fully depressed and crank the engine on the starter motor for several revolutions. Record the reading. Zero the tester and check the remaining cylinders in the same way. All four compression figures should be approximately equal and within the tolerance given in the Specifications. If they are all low, suspect piston ring or cylinder bore wear. If only one reading is down, suspect a valve not seating.
Crankshaft and bearings
8 Examine the crankpin and main journal
surfaces for signs of scoring or scratches.
Check the ovality of the crankpins at different positions with a micrometer. If more than 0.001 inch (0.025 mm) out of round, the crankpins will have to be reground. They will also have to be reground if there are any scores or scratches present. Also check the journals in the same fashion.
9 Wear in a crankshaft can be detected while the engine is running. Big-end bearing and crankpin wear is indicated by distinct metallic knocking, particularly noticeable when the engine is pulling from low engine speeds. Low oil pressure will also occur.
10 Main bearing and journal wear is indicated by engine rumble increasing in severity as the engine speed increases. Low oil pressure will again be an associated condition.
11 Crankshaft grinding should be carried out by specialist engine reconditioners who will supply the matching undersize bearing shells to give the required running clearance.
12 Inspect the connecting rod big-end and main bearing shells for signs of general wear, scoring, pitting and scratching. The bearings should be matt grey in colour.
13 If a copper colour is evident, then the bearings are badly worn and the surface material has worn away to expose the underlay.
Renew the bearings as a complete set.
14 At the time of major overhaul it is worthwhile renewing the bearing shells as a matter of routine even if they appear to be in reasonably good condition.
15 Bearing shells can be identified by the marking on the back of the shell. Standard sized shells are usually marked STD or 0.00.
Undersized shells are marked with the undersize such as 0.25 mm.
Connecting rods
16 Check the alignment of the connecting
rods visually. If you suspect distortion, have
them checked by your dealer or engine
reconditioner on the special jig which he will
have.
17 The gudgeon pin is an interference fit in the connecting rod small-end and removal or refitting and changing a piston is a job best left to your dealer or engine reconditioner due to the need for a press and jig and careful heating of the connecting rod.
Pistons and piston rings 18 If the cylinders have been rebored, then the reconditioner will supply the oversize pistons and rings and the gudgeon pins. Give the job of fitting the new pistons to the connecting rods to him.
19 If the original piston rings or just new rings are to be fitted to the original pistons, use great care to remove and fit the rings as they are easily broken if expanded too much.
Always remove and fit rings from the crown end.
20 If three old feeler blades are slid behind the piston rings and located at equidistant points, the rings may be removed or fitted without their dropping into the wrong grooves and will reduce the chance of breakage (photo).
18.20 Using feeler blades to fit piston rings
21 If the original pistons are being refitted, make sure that the ring grooves and their oil return holes are cleaned out and freed from carbon. A piece of piston ring is a useful tool for this purpose.
22 The three pistons rings are as follows: Top - Thinner compression marked TOP Second - Thicker compression, step at base Bottom - Oil control (photo)
18.22 Piston ring marking
23 If proprietary wear control rings are to be fitted to overcome bore wear, fit them strictly in accordance with the manufacturer’s instructions.
24 Always check the piston ring groove clearance and end gap. Both clearances should be checked with a feeler gauge. Check the end gap when the ring has been pushed squarely down the cylinder bore for two or three inches (photos).
18.24A Checking piston ring groove clearance
18.24B Checking piston ring end gap
25 If new rings are being used and the cylinder bores have not been rebored, always make sure that the top compression ring has been stepped to prevent it contacting the bore wear ridge.
Flywheel
26 Check the clutch mating surface of the
flywheel. If it is deeply scored (due to failure to
renew a worn driven plate) then it may be
possible to have it surface ground provided
the thickness of the flywheel is not reduced
too much.
27 If lots of tiny cracks are visible on the surface of the flywheel then this will be due to overheating caused by slipping the clutch or “riding” the clutch pedal.
28 With a pre-engaged type of starter motor it is rare to find the teeth of the flywheel ring gear damaged or worn but if they are, then the ring gear will have to be renewed.
29 To remove the ring gear, drill a hole between the roots of two teeth taking care not to damage the flywheel and then split the ring with a sharp cold chisel.
30 The new ring gear must be heated to between 180 and 220ºC (356 and 428ºF) which is very hot, so if you do not have facilities for obtaining these temperatures, leave the job to your dealer or engine reconditioner.
31 Where such facilities are available, then the ring gear should be either pressed or lightly tapped gently onto its register and left to cool naturally, when the contraction of the metal on cooling will ensure that it is a secure and permanent fit. Great care must be taken not to overheat the ring gear, as if this happens its temper will be lost. A clutch input shaft pilot bearing is not fitted on this engine.
Camshaft
32 Examine the camshaft bearings for wear,
scoring or pitting. If evident then the bearings
will have to be renewed. The three bearings
are of different sizes and they can be removed
and new ones fitted using a bolt, nut and
distance pieces. When drawing a new bearing
into position, make sure that the oil hole is
correctly aligned with the one in the
crankcase. The centre and rear bearings
require reaming after fitting, the bearing at the
timing chain end is supplied ready reamed
(photo).
18.32 Camshaft bearing
33 The camshaft itself should show no marks or scoring on the journal or cam lobe surfaces. Where evident, renew the camshaft or have it reprofiled by a specialist reconditioner.
34 Check the teeth of the camshaft sprocket for wear. Renew the sprocket if necessary.
Cam followers
35 Examine the bearing surface of the cam
followers which are in contact with the
camshaft. Any indentations or cracks must be
rectified by renewal. Clean sludge and dirt
from the cam followers and check their fit in
their bores. Side to side rock is unusual
except at very high mileage.
Timing chain
36 Examine the teeth on both the crankshaft
sprocket and the camshaft sprocket for wear.
Each tooth forms an inverted “V” with the sprocket periphery and if worn, the side of each tooth under tension will be slightly concave in shape when compared with the other side of the tooth, ie; one side of the inverted “V” will be concave when compared with the other. If any sign of wear is present the sprockets must be renewed.
37 Examine the links of the chain for side slackness and particularly check the self-tensioning links for freedom of movement. Renew the chain if any slackness is noticeable when compared with a new chain. It is a sensible precaution to renew the chain at about 60 000 miles (96 000 km) and at a lesser mileage if the engine is stripped down for a major overhaul.
Cylinder head
38 This is covered in Section 17.
Rockers and rocker shaft 39 Thoroughly clean out the rocker shaft. As it acts as the oil passages for the valve gear, clean out the oil holes and make sure they are quite clear. Check the shaft for straightness by rolling it on a flat surface. If it is distorted, renew it.
40 The surface of the shaft should be free from any wear ridges caused by the rocker arms. If it is not, the shaft will have to be renewed. Blocked shaft oil holes often contribute to such wear.
41 Check the rocker arms for wear of the rocker bushes, for wear at the rocker arm face which bears on the valve stem, and for wear of the adjusting ball ended screws. Wear in the rocker arm bush can be checked by gripping the rocker arm tip and holding the rocker arm in place on the shaft, noting if there is any lateral rocker arm shake. If any shake is present, and the arm is very loose on the shaft, remedial action must be taken. It is recommended that a worn rocker arm be taken to your local FIAT agent or automobile engineering works to have the old bush drawn out and a new bush fitted (photo).
18.41 Rocker components
42 Check the tip of the rocker arm where it bears on the valve head, for cracking or serious wear on the case hardening. If none is present the rocker arm may be refitted. Check the pushrods for straightness by rolling them on a flat surface.
Oil pump
43 Unscrew the four securing bolts which
connect the two halves of the pump body.
44 Clean all the components in a bath of paraffin and dry them.
45 Inspect the gears for wear or damage and then check for wear in the following way.
46 Insert a feeler blade between the tooth peak and the body. This should be between 0.05 and 0.14 mm (0.0019 and 0.0055 in).
47 Now place a straight-edge across the body flange and check for gear endfloat. This should be between 0.020 and 0.105 mm (0.0008 and 0.0041 in). Where the clearances exceed the specified limits, renew the pump.
48 Check that the oil pressure relief valve spring is in good condition and not deformed.
Oil seals and gaskets
49 It is recommended that all gaskets and oil
seals are renewed at major engine overhaul.
Sockets are useful for removing or refitting oil seals. An arrow is moulded onto some seals to indicate the rotational direction of the component which it serves. Make sure that the seal is fitted the correct way round to comply with the arrow.
Fig. 1.25 Checking a crankpin (Sec 18)
Fig. 1.26 Piston/connecting rod relationship (Sec 18)
Fig. 1.27 Exploded view of oil pump (Sec 18)




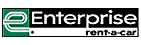
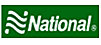

