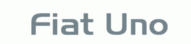
Fiat Uno Manual
Ignition systemSupplement: Revisions and information on later models / Ignition system
General
1 The ignition systems dealt with in this
Section are all fully electronic and are referred
to individually according to type as the
“breakerless”, Microplex and Digiplex 2
system. The Microplex system is used on the
1301 and 1372 cc Turbo ie engines, the
Digiplex 2 on the 1372 cc ie engine and the
“breakerless” system on all other models.
Ignition timing
(all later models)
2 The ignition timing check on all systems
covered in this Section is made using a
stroboscope, connected up in accordance with
the manufacturer’s instructions and pointed at
one of the two positions given below (photos).
10.2A Flywheel timing marks (999 cc engine)
10.2B Flywheel timing marks (1372 cc ie engine)
a) The timing marks on the crankshaft pulley and the timing cover. The right-hand underwing shield will need to be detached and removed to allow access to view these marks (see photos 7B.27 and 7B.30B in this Chapter).
b) The timing marks on the flywheel and the clutch housing. The rubber plug will need to be extracted for access to these marks.
3 A dwell angle check is not possible on any of these systems.
4 When making the stroboscopic ignition timing check it is necessary to disconnect the vacuum hose from the distributor or inlet manifold to module (as applicable) and plug it.
The engine must be at its normal operating temperature and running at the normal specified idle speed when making the check.
Refer to the appropriate part of the Specifications at the start of this Chapter for the idle speed and ignition settings.
Breakerless ignition system -
description
5 On 903 cc engines, the distributor is driven
from an extension of the oil pump driveshaft
which is geared to the camshaft.
6 On 999, 1108 and 1372 cc engines, the distributor is driven from the rear end of the camshaft.
7 On the 1116 and 1299/1301 cc engines, the distributor is driven from an extension of the oil pump driveshaft which is geared to the auxiliary shaft.
8 The distributor contains a reluctor mounted on its shaft, and a magnet and stator fixed to the baseplate.
9 Ignition advance is controlled in the conventional way mechanically by centrifugal weights and a diaphragm unit for vacuum advance.
10 Instead of the conventional method of interrupting the low tension circuit to generate high tension voltage in the coil by means of a mechanical contact breaker, when the electronic ignition is switched on, the switching of the transistors in the electronic control unit (ECU) prevents current flow in the coil primary windings.
11 Once the crankshaft rotates, the reluctor moves through the magnetic field created by the stator and when the reluctor teeth are in alignment with the stator projections a small AC voltage is created. The ECU amplifies this voltage and applies it to switch the transistors and so provide an earth path for the primary circuit.
12 As the reluctor teeth move out of alignment with the stator projections the AC voltage changes, the transistors in the ECU are switched again to interrupt the primary circuit earth path. This causes a high voltage to be induced in the secondary winding.
Distributor
(breakerless type) -
removal and refitting
13 Removal of the distributor on the 903,
1116, 1299 and 1301 cc engines is as
described in Chapter 4, Section 6.
14 On 999, 1108 and 1372 cc engines, mark the position of the distributor clamp plate in relation to the cylinder head surface.
15 Unclip the distributor cap and move it to one side with the HT leads attached.
16 Disconnect the LT lead plug and, where applicable, the vacuum hose (photo).
10.16 Distributor LT lead connecting plug
17 Unscrew the distributor fixing nuts and withdraw the unit.
18 The distributor drive is by means of an offset dog no special procedure is required to refit it. Providing the dog engages in its slot and the distributor body is turned to align the marks made before removal, the timing will automatically be correct.
19 If a new distributor is being fitted (body unmarked), set No. 4 piston at TDC (0º) by turning the crankshaft pulley bolt until the timing marks on the crankshaft pulley and engine front cover are in alignment.
20 Align the drive dog and fit the distributor then turn the distributor body until the contact end of the rotor is aligned with the arrow on the distributor dust shield.
21 Tighten the distributor clamp nuts. Refit the cap and disconnected components and then check ignition timing using a stroboscope.
Distributor (breakerless
type) - overhaul
22 It is recommended that a worn out or
faulty distributor is renewed. However,
individual components such as the cap, rotor,
reluctor, magnet/stator/baseplate assembly,
vacuum diaphragm unit, and drive gear or dog
are available separately.
Breakerless
ignition system
components - testing
23 A voltmeter and an ohmmeter will be
required for this work.
Primary circuit voltage
24 Turn on the ignition, and using a voltmeter
check the voltage at the ignition coil LT
terminals. Any deviation from battery voltage
will indicate a faulty connection, or if these are
satisfactory, then the coil is unserviceable.
Magnetic impulse generator winding 25 Remove the distributor and ECU and disconnect their connecting leads.
26 Connect an ohmmeter to the impulse generator terminals and note the reading. The resistance should be as given in the Specifications at the beginning of this Chapter.
27 Now check between one of the impulse generator terminals and the metal body of the distributor. Infinity should be indicated on the ohmmeter. If it is not, renew the impulse generator carrier plate. Note: When carrying out this test it is imperative that the connections are remade as originally observed. Also ensure that there is no possibility of the ECU supply (red) cable and earth cable making contact in service.
Ignition coil winding resistance 28 Check the resistance using an ohmmeter between the coil LT terminals. Refer to the Specifications for the expected coil resistance.
29 Check the resistance between the LT lead socket on the coil and each of the LT terminals. Refer to the Specifications for the expected coil resistance.
30 The rotor arm resistance should be approximately 5000 ohms.
Microplex ignition system -
description
31 This system is fitted to the 1301 and
1372 cc Turbo ie models, and comprises the
following components.
Electro-magnetic sensors 32 Two sensors are used to pick up engine speed and TDC position directly from the crankshaft.
Pressure and vacuum sensor 33 This converts inlet manifold vacuum pressure into an electrical signal for use by the electronic control unit (ECU).
Anti-knock sensor
34 This converts “pinking” detonations which
occur within the combustion chambers into
an electrical signal for use by the ECU (photo).
10.34 Anti-knock sensor
10.35 Ignition ECU on rear bulkhead (1301 cc Turbo ie engine)
Electronic Control Unit (ECU) 35 This computes the optimum ignition advance angle from the sensor signals received, and controls the action of the ignition unit (photo).
Ignition unit
36 This comprises four elements (photo).
10.36 Ignition coil (1) and power module (2) on 1301 cc Turbo ie engine
a) Power module - receives the ignition advance command and controls the conduction angle of the primary current and energy stored in the coil.
b) Dissipater plate - eliminates the heat which is generated by the high volume of current.
c) Ignition coil with low primary resistance.
d) Distributor - a means of distributing high tension to the spark plugs. The rotor is driven in an anti-clockwise direction (viewed from transmission) by a dog on the end of the camshaft.
37 The system incorporates a safety pressure switch, which cuts out the ignition if the turbocharging pressure exceeds a value of between 0.84 and 0.93 bars (12.2 and 13.5 lbf/in2) above atmospheric pressure.
Distributor (Microplex) -
removal and refitting
38 Remove the distributor cap and place it to
one side, complete with spark plug leads
(photo).
10.38 Removing the distributor cap
39 Turn the crankshaft by means of the pulley nut, or by raising and turning a front wheel with top gear engaged, until No. 4 piston is on its firing stroke. This will be indicated when the contact end of the rotor arm is aligned with the mark on the distributor body rim, and the lug on the crankshaft pulley is aligned with the timing pointer on the engine. The right-hand underwing shield will have to be removed in order to see the marks (photo).
10.39 Crankshaft pulley timing marks (arrowed)
40 Unscrew the distributor fixing nuts and withdraw the distributor.
41 When fitting the distributor, the offset drive dog will automatically locate the distributor rotor in its correct position, but the distributor body may require rotating in order to align the rim mark with the rotor. The elongated slots for the fixing studs are to permit initial alignment, not for subsequent adjustment, as advance angle alterations are carried out automatically by the system ECU (photos).
10.41A Distributor body showing elongated slots in the mounting lugs
10.41B Distributor drive dog
42 Tighten the nuts and refit the cap with leads.
43 Unless a stroboscope and a vacuum pressure gauge are available, it will not be possible to check the advance values with the engine running. Where these instruments are available, connect the vacuum gauge to the inlet manifold, and the stroboscope in accordance with the equipment manufacturer’s instructions. Refer to Fig. 13.79 according to the inlet manifold vacuum pressure indicated.
Microplex ignition system
components - testing
44 An ohmmeter and a voltmeter will be
required for these tests.
45 Remove the multipin plug from the ECU.
Engine speed sensor
46 Insert the probes of an ohmmeter
between terminals 3 and 16 of the multipin
connector; 618 to 748 ohms (1301 cc) or
578 to 782 ohms (1372 cc) should be
indicated.
47 If necessary, carry out a check of the gap between the sensor and flywheel teeth as described in Chapter 4, Section 10.
TDC sensor
48 Insert the probes of the ohmmeter
between terminals 1 and 2 of the multipin
connector; 618 to 748 ohms (1301 cc) or 578
to 782 ohms (1372 cc) should be indicated.
49 If necessary, carry out a check of the gap between the sensor and the crankshaft pulley, as described in Chapter 4, Section 10.
ECU supply
50 Switch on the ignition, and then insert the
probes of a voltmeter between terminals 13
and 11 of the multipin connector. Battery
voltage should be indicated. If not, check the
battery earth, ignition switch or intermediate
connector plug for security.
Power module supply (1301 cc) 51 Pull the multipin plug from the power module, and connect the probes of a voltmeter between terminal 4 of the connector and earth. If the reading is less than battery voltage, check the security of all connections between the ignition switch and terminal + 15 of the ignition coil.
52 Reconnect the multipin connector to the ECU, but have the one from the power module disconnected, and then switch on the ignition.
53 Connect the voltmeter between terminals 4 and 2 of the power module multipin connector. If the indicated voltage is less than battery voltage, check the security of all connections between the ignition switch and terminal + 15 of the ignition coil, and the battery earth. If all are satisfactory, check for continuity between terminals 11 and 12. If continuity is broken, renew the ECU.
Power module (1372 cc)
54 Proceed as described in paragraph 53.
Anti-knock sensor
55 If “pinking” occurs, or loss of power is
noticed, test the sensor by substitution of a
new one.
Ignition coil
56 Disconnect the leads from terminals 1
and 15 on the coil before testing.
57 Using the ohmmeter, check the resistance of the primary winding. This should be between 0.31 and 0.37 ohms (1301 cc) or 0.40 to 0.49 ohms (1372 cc), at an ambient temperature of 20ºC (68ºF).
58 The secondary winding resistance should be between 3330 and 4070 ohms (1301 cc) or 4320 to 5280 ohms (1372 cc), at an ambient temperature of 20ºC (68ºF).
Distributor
59 Check the resistance of the rotor arm,
which should be between 800 and
1200 ohms.
60 Where all the foregoing tests have proved satisfactory, then any problem must be due to a fault in either the power module or the ECU.
These components can only be checked by the substitution of a new unit - power module first, then the ECU.
Safety pressure switch
61 The device protects the engine from
excessive turbocharging pressure, cutting off
the ignition by earthing the Microplex ECU.
Testing is not possible without a special pressure pump, so the easiest way to check a suspected fault is to fit a new unit.
Digiplex 2 ignition system -
description
62 This system operates in a similar manner
to that of the earlier type described in Chapter
4, but the circuit layout differs to suit the
Mono Jetronic fuel injection system. In
operation, the main difference is that the
Digiplex 2 system has a greater number of
advance points than the earlier system.
Comparison of Fig. 13.82 with Fig. 4.2 illustrates the difference in layout. Note that the distributor is mounted on the rear end of the cylinder head and is driven by the camshaft.
63 When working on the Digiplex 2 ignition system or associated components, the precautionary notes outlined in Section 9 of Chapter 4 must be adhered to.
64 As with the earlier system, test procedures possible on the Digiplex 2 system are restricted due to the need for specialised testing equipment. The following checks are possible, however, using a conventional test meter.
Ignition coil check
65 To check the resistance of the coil’s
primary windings, connect the probes of an
ohmmeter between the positive terminal and
the negative terminal as shown in Fig. 13.83,
and check that the resistance reading at 18 to
28ºC is 0.45 ohms ± 10% (photo).
10.65 Ignition coil and connections on the 1372 cc ie engine
66 To check the resistance of the coil’s secondary windings, connect the probes of an ohmmeter between the positive terminal and the HT lead terminal as shown in Fig. 13.84.
Check that the resistance reading at 18 to 28ºC (64 to 82ºF) is 4800 ohms ± 10%.
Ignition timing check
67 Refer to paragraph 2 in this Section.
Engine speed and TDC sensor check 68 To check the resistance between the sensor and the ECU, detach the wiring connector (photo). Connect the probes of an ohmmeter to the connector terminals and check that the resistance reading is between 600 and 760 ohms at 20ºC (68ºF). If the reading is not as specified, the sensor must be renewed.
10.68 ECU location on the 1372 cc ie engine
69 The gap between the sensor and the pins on the rear face of the flywheel must be between 0.2 and 0.8 mm. Any deviation outside of this clearance will be due to mechanical damage to the sensor and necessitates its renewal. The sensor is accurately positioned during manufacture and secured with tamperproof screws; it does not require any adjustment during servicing. If it is necessary to renew the sensor, a special gap setting tool is required and the task is therefore best entrusted to a FIAT dealer.
Distributor (Digiplex Z) -
removal and refitting
70 Proceed as described in paragraphs 14
to 21. When refitting the distributor, ensure that
the engine is still set at the TDC position. Engage
the rotor arm into position on the shaft so that its
lug engages in the slot in the top end of the drive
spindle. Align the rotor arm with the reference
slot on the edge of the distributor housing as
shown in Fig. 13.85, then fit the distributor into
position and secure with the retaining nuts
(photo). As previously mentioned, the fine timing
is made automatically through the ECU.
10.70 Ignition distributor and HT lead connections on the 1372 cc ie engine
Spark plugs and HT leads -
general
71 Copper-cored spark plugs are now fitted
to all models. The recommended types are
given in the Specifications Section of this
Supplement.
72 The HT lead connection sequence to the distributor cap on the 999 and 1108 cc engines is shown in Fig. 13.86. That for the 1301 cc Turbo ie is as shown (photo).
10.72 HT lead connecting sequence on the 1301 cc Turbo ie engine
Fig. 13.70 Breakerless ignition system - 999 and 1108 cc engines (Sec 10)
1 Battery
2 Ignition switch
3 Ignition coil
4 Coil HT lead
5 Distributor
6 ECU
7 LT cables
8 Vacuum advance unit
9 Spark plug HT leads
10 Spark plugs
11 Vacuum hose
Fig. 13.71 Location of electronic ignition components on early models with
breakerless ignition (Sec 10)
1 ECU
2 Ignition coil
3 Distributor
4 Vacuum advance unit
5 Pick-up filter with calibrated opening for atmospheric pressure
Fig. 13.72 Rotor aligned with arrow on distributor dust shield - 999 and 1108
cc engines (Sec 10)
Fig. 13.75 Microplex ignition system components on the 1301 cc Turbo ie
engine (Sec 10)
1 ECU
2 Safety pressure switch
3 Ignition unit and coil
4 Distributor
5 Anti-knock sensor
S1 TDC sensor
S2 Engine speed sensor
Fig. 13.76 Microplex ignition system components on the 1372 cc Turbo ie
engine (Sec 10)
Fig. 13.73 Wiring diagram of the Microplex ignition system on the 1301 cc
Turbo ie engine (Sec 10)
1 ECU
2 Safety pressure switch
3 Ignition unit with coil
4 Distributor
5 Anti-knock sensor
6 Vacuum/pressure pick-up in engine inlet manifold
7 Socket for diagnostic equipment
8 Tachometer
9 Spark plugs
10 Switch to earth (to retard advance curve if necessary)
11 Turbocharger operation warning light
12 Anti-theft relay (where fitted)
13 Hidden anti-theft switch (where fitted)
Fig. 13.74 Wiring diagram of the Microplex ignition system on the 1372 cc
Turbo ie engine (Sec 10)
1 ECU
2 Pipe (pressure/vacuum in inlet manifold to control unit)
3 Spark plug
4 Distributor
5 Ignition coil (with control unit)
6 Tachometer
7 Ignition switch
8 Connector
9 TDC sensor
10 Engine speed
11 Anti-knock sensor
12 Air pressure safety switch
13 Speedometer signal for electronic injection
14 Connector
15 Diagnostic socket
a Crankshaft pulley
b Flywheel
Fig. 13.77 Crankshaft pulley timing mark aligned with timing pointer -
Microplex ignition system (Sec 10)
1 TDC sensor
Fig. 13.78 Rotor aligned with distributor body rim mark - Microplex ignition
system (Sec 10)
Fig. 13.79 Ignition advance curves - Microplex ignition system on the 1301 cc
Turbo ie (Sec 10)
Fig. 13.80 Microplex ignition system ECU multipin connector (Sec 10)
For colour code, see main wiring diagrams
Fig. 13.81 Microplex ignition system control unit connection (Sec 10)
For colour code, see main wiring diagrams
Fig. 13.82 Digiplex 2 ignition system wiring circuits and components (Sec 10)
Fig. 13.83 Test connections for ignition coil primary windings check -
Digiplex 2 ignition system (Sec 10)
Fig. 13.84 Test connections for ignition coil secondary windings check -
Digiplex 2 ignition system (Sec 10)
Fig. 13.85 Rotor arm must align with slot (1) in distributor housing when
refitting distributor - Digiplex 2 ignition system (Sec 10)
Fig. 13.86 HT lead connections on distributor cap of the 999 and 1108 cc
engines (Sec 10)




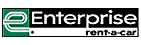
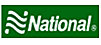

